La digitalizzazione fa aumentare la competitività
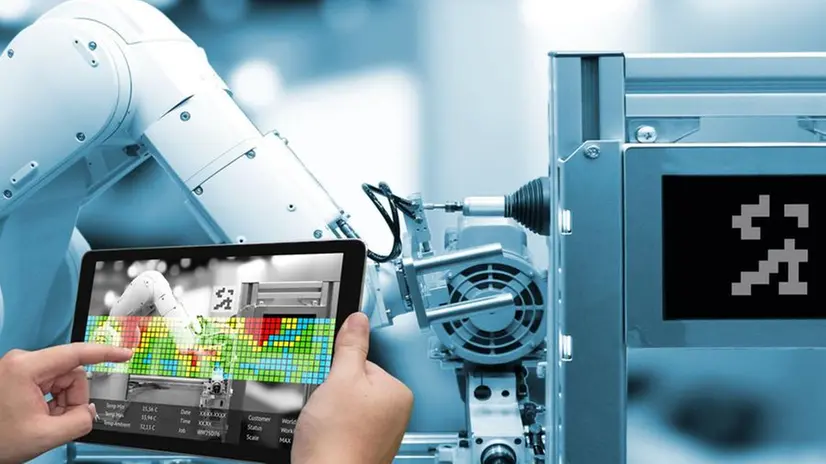
È difficile ottenere una stima dettagliata del livello di digitalizzazione delle aziende manifatturiere. L’ultima ricerca su questo tema risale a maggio 2024 ed è la «Smart Manufacturing Survey 2024», l’indagine svolta da Tig – The Innovation Group in collaborazione con Sps Italia e Contact Value. L’indagine ha rivelato che, nel 2023, il 47% delle industrie ha investito in progetti di cybersecurity e data analytics.
I dati
Tra le tecnologie più adottate nel percorso verso il paradigma Industria 4.0 spiccano il cloud. Computing e i Mes, con il 42% delle imprese intervistate che ha dichiarato di aver investito in queste soluzioni. L’Internet of Things (IoT) segue con un tasso di investimento del 33%. Tuttavia, il dato più interessante è che solo un modesto 18% di queste aziende utilizza i dati raccolti attraverso tecnologie come IoT e Data Analytics in modo diffuso, mentre il 33% afferma di non averli utilizzati affatto.
Queste aziende hanno poi dichiarato che, per affrontare le sfide della trasformazione verso un modello di Data-Driven Manufacturing, sarà necessario investire non solo in infrastrutture e tecnologie, ma anche nella formazione e, più in generale, nel cambiamento della cultura aziendale.
Questi dati non mi hanno sorpreso. Dalla mia esperienza trentennale nell'installazione di sistemi Mes, ho osservato una correlazione chiara tra le aziende che credono nella digitalizzazione della produzione e una posizione di leadership nel loro mercato di riferimento. Digitalizzare non significa semplicemente introdurre tecnologia o collaborare con un partner adeguato, aspetti certamente fondamentali, ma non sufficienti da soli.
È necessario, prima di tutto, un cambiamento culturale. Automatizzare la raccolta dei dati, senza poi analizzarli correttamente o apportare i cambiamenti tecnici e organizzativi che essi suggeriscono, significa non sfruttare appieno la tecnologia. Questo atteggiamento rischia di portare, prima o poi, all’abbandono degli strumenti, percepiti come inutili. Implementare sistemi Mes 4.0/5.0 solo per ottenere un beneficio fiscale non migliora la competitività: è come acquistare una macchina con lo sconto, senza però trarre il massimo valore dall’investimento.
La sfida culturale
Nella mia esperienza, la principale sfida da superare è quella culturale: non credere nei dati di produzione significa trattare ogni strumento come equivalente, accettare qualsiasi approccio e non intraprendere le necessarie azioni di miglioramento. In altre parole, il digitale finisce per essere considerato un costo, anziché un fattore strategico per aumentare la competitività.
Il piano 5.0 si basa su un elemento essenziale: la misurazione accurata dei consumi e l’integrazione dei dati tra tutti i sistemi aziendali. Per questo, un’industria 5.0 deve prima di tutto essere un’industria 4.0, con processi misurabili, informazioni integrate in tempo reale e condivise tra i vari sistemi.
Step 1: essere 4.0
Sebbene sia fondamentale misurare i consumi di ogni macchina o impianto, questa misurazione fine a se stessa non è sufficiente per raggiungere lo standard 5.0. Essa rappresenta solo una certificazione del risultato e non fornisce le informazioni necessarie per un miglioramento continuo dei processi. Ecco perché, prima di tutto, è necessario essere 4.0, ovvero dotarsi di sistemi Erp, Plm e Mes integrati, in grado di misurare l’efficienza dei processi e correlare tali dati con l’efficienza energetica.
La misurazione, sia dell’efficienza sia dei consumi energetici, permette di calcolare il costo energetico per prodotto e di identificare le perdite produttive più rilevanti per macchina, attrezzatura, articolo o operazione. I sistemi Mes possono essere visti come una vera e propria «cassetta degli attrezzi» dotata di tre strumenti fondamentali.
Il primo è una lente, che consente di individuare tutte le perdite e le possibili ottimizzazioni nei processi produttivi, permettendo di attuare azioni correttive e preventive. Il secondo è un calibro, che consente di misurare con precisione e da prospettive diverse (per tempo, macchina, articolo, attrezzatura) i benefici derivanti dalle azioni correttive o dalla sostituzione di macchinari. Il terzo è un veicolo, che connette sistemi differenti, integrando le informazioni lungo tutta la supply chain, rendendo così più efficaci anche i portali di gestione energetica.
Claudio Morbia, ad Lutech-Stain
Riproduzione riservata © Giornale di Brescia
Iscriviti al canale WhatsApp del GdB e resta aggiornato
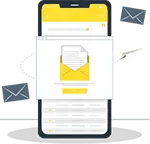
@Economia & Lavoro
Storie e notizie di aziende, startup, imprese, ma anche di lavoro e opportunità di impiego a Brescia e dintorni.