Strategia Beretta: interconnessione per competere ovunque
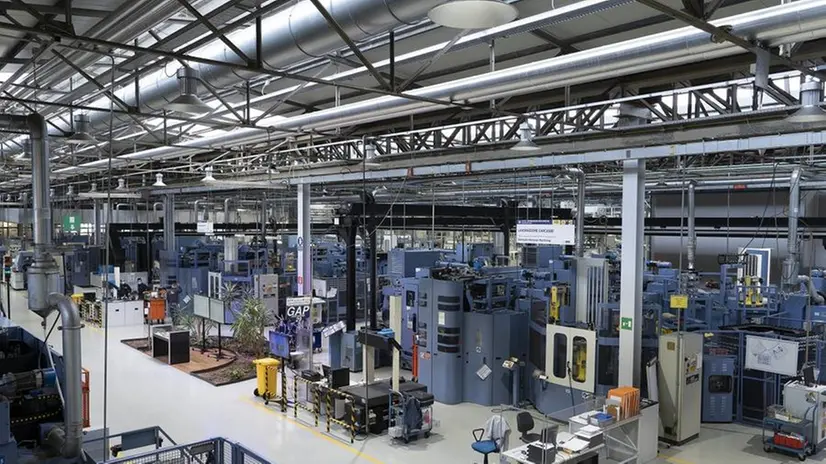
Mettersi in gioco, sempre. La strada per il miglioramento continuo e per il successo non è percorribile da chi si adagia sugli allori cullato dai propri risultati. In un’epoca in cui i cambiamenti si susseguono uno dietro l’altro, ripensare il proprio modo di operare è la strada per continuare a competere. Anche per chi ha 500 anni di storia alle spalle.
La Fabbrica d’Armi Pietro Beretta di Gardone Valtrompia ha annunciato sul finire dell’anno scorso un piano di interventi trasversale, denominato «Beretta digital 500», che interesserà tutti gli ambiti operativi (progettazione, produzione, supply chain, sales and marketing e risorse umane), ovviamente sotto l’egida delle nuove tecnologie digitali. Lo sforzo economico è imponente: oltre 5 milioni di euro in autofinanziamento che la Fabbrica d’Armi Pietro Beretta stanzia ogni anno per il digitale unitamente agli undici milioni in tre anni (20 per cento a fondo perduto e 60 per cento finanziata a tasso vantaggioso) che arriveranno dal Ministero dello Sviluppo economico per sostenere quell’idea ben enunciata dal presidente della storica impresa Franco Gussalli Beretta: «La missione che spetta alla mia generazione è quella di fare del digitale la spina dorsale dell’azienda».
Questa volontà si concretizzerà attraverso specifici e pervasivi interventi di innovazione e implementazione. Per quanto concerne la progettazione, la prassi di virtualizzare la prototipazione, prima ancora di realizzare un «prototipo» fisico, verrà ulteriormente approfondita, per testare digitalmente i modelli al fine di verificarne ex ante comportamenti fluidodinamici e meccanici. Sul fronte della produzione il fulcro è indubitabilmente il Beretta Intelligence Manufacturing System, un’architettura software in grado di collettare, validare e visualizzare dati sui quali prendere decisioni strategiche o di miglioramento dei processi: ciò si concretizza in un’applicazione basata su mappe, in stile Google Maps, dove è possibile individuare, analizzare e sistemare situazioni anomale.
A ciò si aggiungono altre implementazioni in diverse fasi del processo produttivo, dalla sensorizzazione e interconnessione di 146 macchine a controllo numerico al monitoraggio dei consumi delle stesse tramite una rete IoT basata sul protocollo LoRaWan (con A2A e Csmt). Nell’immediato futuro ci sar inoltre l’adozione di nuovi algoritmi di intelligenza artificiale, al fine di realizzare i completo digital twin della fabbrica. Importanti anche gli interventi sulla supply chain (integrando tramite l’It le varie componenti della catena) e sul lato vendite e marketing. Una strategia quindi molto complessa e innovativa.
Riproduzione riservata © Giornale di Brescia
Iscriviti al canale WhatsApp del GdB e resta aggiornato