Legno e poliuretano: pannelli Ilpa sul tetto del mondo
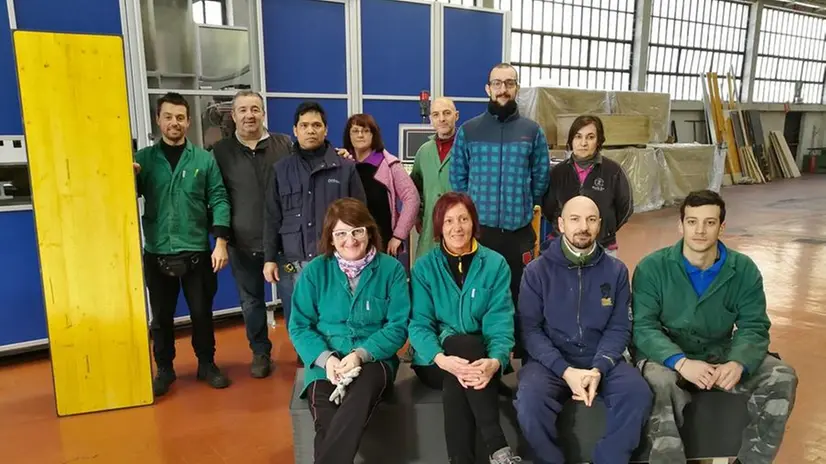
Tra qualche anno, nell’aula di una facoltà di Economia, l’esperienza della Ilpa srl di Nave potrebbe tranquillamente essere usata come caso di studio. Ha superato la crisi, quella durissima del settore edilizio dove opera producendo pannelli in legno per casseforme, ha fatto dell’innovazione e della collaborazione con altre imprese i suoi punti di forza, il suo business è esteso in tutto il mondo.
I suoi prodotti - solo per fare una sintetica rassegna - sono stati o sono utilizzati per realizzare i grattacieli Hudson Yards a New York, l’area di Barangaroo a Sydney, il Mose a Venezia e la Kingdom Tower a Gedda in Arabia Saudita, primo edificio al mondo a superare il chilometro di altezza.

Tutto questo in un’azienda da 5 milioni di fatturato e 13 dipendenti, una pmi che dal 1948 ha il suo quartier generale nell’ex distretto del tondino valtrumplino. «Dal 2008 in poi abbiamo sofferto molto ma siamo riusciti a sopravvivere, rimanendo l’unica realtà in Italia a produrre i pannelli utilizzati per le colate di cemento - spiega il titolare Rubens Pasotti -. Ora i nostri competitor sono solo attori internazionali e il nostro mercato guarda all’India così come agli Stati Uniti e al Sudafrica».
Ed è proprio da questo paese che riparte il futuro dell’Ilpa. «Nei giorni scorsi abbiamo spedito il primo di tre container destinati ad un’azienda del posto - conferma Pasotti -. Si tratta della fornitura di un nuovo prodotto, sviluppato dopo anni di ricerca e che ha visto la luce qualche settimana fa».
La novità in questione è un pannello con anima in legno (multistrato in betulla) rivestito in polipropilene (peculiarità dell’Ilpa ideata negli anni ’90 e sviluppata insieme al colosso tedesco Doka). Il plus che è pronto a rilanciare il business aziendale, con previsioni di fatturato in crescita del 20% già dal 2017, è però dato dal bordo con il quale è rivestito: uno strato di poliuretano, che facilita l’assemblaggio della gabbia in acciaio dove viene colato il cemento e soprattutto rende meno deperibile agli urti e all’erosione il pannello.
«Far aderire la plastica al legno è un’operazione molto complessa e ci ha portato a dover modificare radicalmente il processo di realizzazione - dice Pasotti -. Per rendere possibile quest’innovazione, che avevamo già pensato anni fa ma non è stata concretizzata prima a causa della crisi, abbiamo sviluppato un nuovo macchinario».
Grazie ad uno sforzo di 700mila euro, che sfrutta le agevolazioni dell’iperammortamento previsto dal Piano Calenda, e alla collaborazione con le ditte OmBattaglio di Nave e Mcs Facchetti di Mura, è stata assemblata ex novo una macchina in grado di creare il pannello sviluppato dai tecnici Ilpa. Per la definizione del piano iperammortamento e quindi per avere le agevolazioni fiscali relative, l’azienda si è affidata alla Ibs Consulting di Brescia.
Per il futuro la Ilpa ha in programma un nuovo investimento, un progetto innovativo per il settore delle casseformi destinate all’edilizia. «Vogliamo ulteriormente migliorare il procedimento di costruzione, eliminando i difetti che necessariamente il cemento presenta quando lo si cola nelle attuali armature - spiega Rubens Pasotti -. Anche in questo caso la plastica ci servirà per diminuire lo spazio tra un pannello e l’altro, riducendo al minimo l’imprecisione del lavoro».
Riproduzione riservata © Giornale di Brescia
Iscriviti al canale WhatsApp del GdB e resta aggiornato